Choosing the Right Crusher for Rock, Stone, Concrete and Asphalt
Feed size, finished product size, and type of material to be crushed are just a few of the things to consider before choosing a crusher. The right choice of a crusher is the first step in optimizing your production.
Choosing the Right Crusher for Rock, Stone, Concrete and Asphalt
View Our Inventory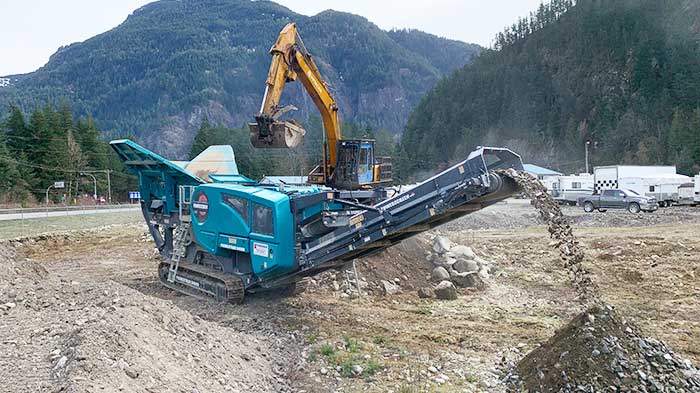
Choosing the right crusher
Aggregate producers and recyclers use rock crushers to reduce the size of rock, stone, concrete and asphalt rubble to produce construction materials like base gravel and new concrete and asphalt mixes.
Several types of crushers are available in the marketplace, but jaw, cone, and impactors are the most commonly used today.
4 Things You Need to Know to Choose the Right Rock Crusher
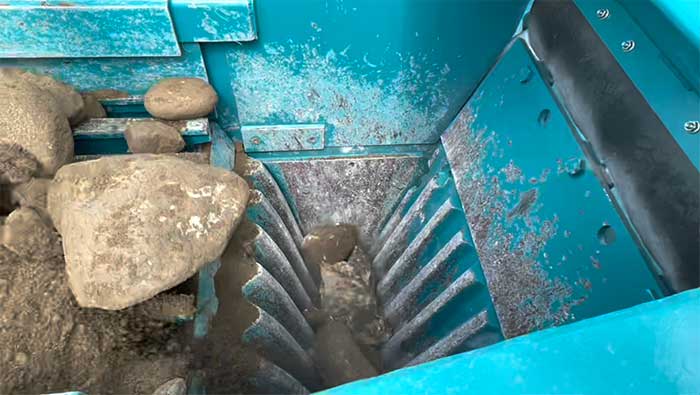
Before You Call or Visit the Dealership — Know Your Material
Before you pick up the phone or head out to the dealership, take a few minutes to gather the key info about your material. It’ll help you (and us) choose the right crusher for the job.
Doing this homework first will save time, money, and ensure you get a machine that delivers exactly what you need
Here’s what you need to know:
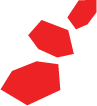
Material Type
Is it abrasive? Hard? The material’s hardness and abrasiveness affect the compressive strength and determine which crusher type is best.
Feed Size
What size is the material going in? This helps determine how big your crusher needs to be.
Finished Product Size
What size do you need the material to be after crushing? This affects how many crushing stages you’ll need.
Capacity (Throughput)
How much material do you need to process per hour? Crushing capacity is usually measured in tons per hour.
Types of rock crusher
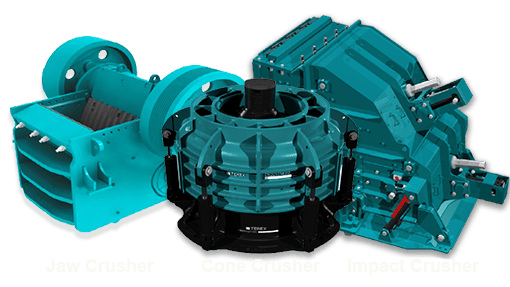
Compression vs. Impact Crushers
All crushers break rock — they just do it differently.
The way a crusher breaks material is what defines it, and it’s the key to choosing the right machine for your job.
Think about it:
There are basically three ways to break something…
- Squeeze it until it shatters – Compression
- Throw it at something hard – Impact
- Smash it with force – also Impact
Compression Crushers
Jaw and cone crushers use brute force to crush rock between two solid surfaces.
Great for: Hard, abrasive materials like granite and basalt
Known for: Durability, high production rates, and consistent performance
Ideal when: You need strength and long wear life
Impact Crushers
These machines use speed and sudden force to break rock inside the chamber.
Great for: Soft to medium-hard materials like limestone and concrete
Known for: High reduction ratios and good shaping
Ideal when: You want fast, efficient crushing and a more refined product
Bottom line?
Compression = Power + Toughness
Impact = Speed + Precision
Still not sure what you need?
We can help you match the right crushing method to your material and goals.
Crusher Configurations: Stationary, Mobile, or Portable?
Crushers don’t work alone. They’re often paired with feeders, hoppers, and conveyors, then mounted on a frame or chassis to create a full crushing plant. Depending on your operation, these plants can be:
Stationary or Modular
Track-mounted Mobile
Wheel Portable
Stationary and Modular Crushing Plants
These setups are common in quarries and mines where the plant is built to stay put. They require significant infrastructure—like concrete pads, retaining walls, ramps, and buildings—to support the equipment.
The downside?
Since the crusher doesn’t move, your feed source (like a working face in a pit or quarry) eventually gets farther away. That leads to:
Longer loader cycle times
Increased fuel burn
More wear and tear on your equipment
As the distance grows, you’ll need to push material with dozers, haul it with trucks, or install long conveyors—each adding cost and complexity.
Wheeled and Track-Mounted Mobile Plants
These offer flexibility. You can reposition them as the jobsite evolves or move them between sites with ease. That means:
Better proximity to your material source
Faster setup and teardown
Easier machine swaps for service or upgrades
Whether you’re managing a remote pit or a high-volume jobsite, portable and mobile setups can save time, cut operating costs, and keep your crew productive.
Mobile vs 🛞 Portable Crushing Plants: What’s the Difference?
Both mobile and portable crushing plants are designed to move—but how they move (and how fast they get to work) can make a big difference in your operation.
There’s no one-size-fits-all answer. The right setup depends on your site, your material, and your crew. But here’s the quick and dirty on both options:
Track-Mounted Mobile Plants
Fast, nimble, and self-contained.
Sets up in minutes, not hours
No external power required
Smaller footprint—great for tight spaces
Perfect for remote or rugged job sites
Easier to reposition during active operations
Mobile plants shine when flexibility is critical and downtime isn’t an option.
Wheel Portable Plants
Flexible, but they need a little prep.
Requires spotting, setup, and external power
Cables must be laid out and connected
Setup time: a few hours to several days, depending on complexity
Larger footprint, but often more modular/customizable
Portable plants have come a long way—and many producers swear by them. But they still need a little more TLC to get rolling.
Bottom Line?
If you need to move fast, work in tight or remote locations, or want a plug-and-play setup, mobile is your go-to.
If you’re planning for larger setups, more custom infrastructure, or longer-term use in a central location, portablecould be the better fit.
Your Mobile Crushing Solutions Provider
Foreman Equipment is your go-to source for mobile, track-mounted crushers in B.C.
We carry a full lineup of jaw, cone, and impact crushers from two of the industry’s top names:
Powerscreen — trusted since 1984
Evoquip — compact crushing and screening specialists
Whether you’re running a full-scale quarry or tackling tight urban job sites, we’ve got the right crusher for the job:
High-capacity primary crushers for pit and quarry operations
Compact, maneuverable crushers for confined spaces and quick setups
Need power, flexibility, and performance on wheels or tracks?
Foreman Equipment delivers.
Whatever you need to crush.
Whether you need to crush 200,000 tonnes in a pit or quarry, or 2,000 tonnes of concrete recycling on a C&D job, we’ve got you covered with reliable, cost-effective crushing equipment from Powerscreen and Evoquip.