Enhance Crusher Performance with Durable OEM Wear Parts
Wear occurs in all crushers, but you can help control costs by choosing the right liner configuration for the desired application. Crusher wear parts from Powerscreen and Evoquip are proven to enhance crusher performance, increase reliability and maximize uptime.
Why Choose OEM Crusher Wear Parts for Maximum Efficiency?
- More than 50 years of field-proven knowledge and experience built into every part.
- All wear parts come with OEM reliability guaranteed from the manufacturer.
- Most manufacturer warranty covers only genuine OEM parts.
Manganese Liner Composition
14% Manganese
In some soft rock applications, 14% manganese can perform better than other grades of manganese.
Under normal conditions, it will work harden but it is not recommended for abrasive and hard rock applications due to the likelihood that excessive wear will occur.
18% Manganese
This grade of manganese is our standard. It performs well in most aggregate and recycling applications. it has an initial hardness of around 230 BHN (Brinell Hardness) but can work harden to 400 BHN during operation.
22% Manganese
Like the 18% manganese, this material has a higher initial hardness of 248BHN.
On hard rock applications, 22% manganese can offer longer wear life, increased uptime and can outperform other grades of material.
Jaw Crusher Liners
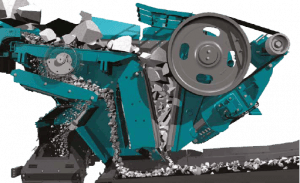
FEATURES & BENEFITS OF OEM JAW LINERS
- 18% Manganese supplied as standard provides results across the broadest range of applications
- A range of tooth profiles allows maximized performance across all applications
- Fully machined on the back and the wedge locating surfaces provides ease of the speed of fitting them
- Convenient, easy lifting system facilitates changes
- All jaw plates are fully reversible, allowing maximum usage of available plate
Jaw Profiles
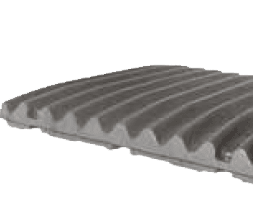
Standard Tooth
Applications
- Pit & Quarry
Recycling – excels in applications where high rebar content is a factor.
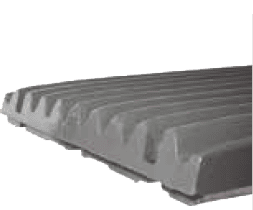
Supertooth
Standard across the Powerscreen jaw crusher range.
Applications
- Quarrying and most recycling applications
- Offers excellent wear life through enhanced profile jaw teeth without compromising strength or product shape.
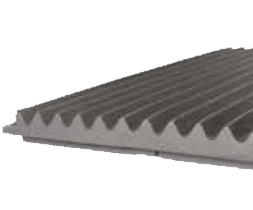
Multitooth
The “sharper” profile makes the Multitooth ideal for most recycling applications, particularly those involving concrete. It is also more tolerant when recycling asphalt.
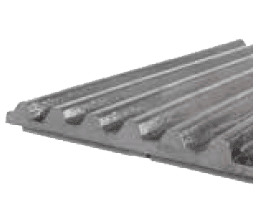
Quarry Tooth
Provides increased wear life due to a deeper and wider tooth profile.
Applications
- Hard rock
- High abrasion
- River gravel
The right wear parts and cone crusher chamber configurations to optimize performance and product.
In all crushing equipment, the choice of wear parts often has a direct impact on the quality of the end product produced – this is especially true for cone crushers where end product specification and quality are of key importance.
With the correct cone wear parts and chamber configurations customers can:
- Maximise energy utilisation
- Avoid peak loads
- Most importantly: avoid uneven and premature wear
- 18% manganese is supplied as standard for Concaves and Mantles across the complete range of Powerscreen cone crushers
- This is a proven material choice across a broad range of applications
- It has an initial hardness of around 230 BHN and can work harden up to approximately 400 BHN.
Cone cavity configurations are totally dependent upon the feed material size, its characteristics and the required product size.
Some of the most popular cone chamber configurations are as follows. The correct choice of configuration depends on the maximum piece size, these are detailed in the table below.
Impactor Blow Bars

The choice of impact crusher blow bar depends entirely on application – the main factors being; maximum feed size, abrasiveness and hardness of the rock.
Martensitic
The martensitic steel blow bar is a good option for the widest variety of
applications and is suitable where there is variable feed material. It demonstrates good impact resistance against all but the hardest rocks and shows high resistance to gouging abrasion.
Supplied at around 500 BHN and does not work harden.
Martensitic steels Martensitic blow bars are less susceptible to damage than Chrome so the material feed size is only restricted by the maximum
chamber feed size.
Chrome
The high chrome blow bar is ideal for highly abrasive applications with no oversize high-impact rocks or recycling debris in the feed. It is not tolerant to tramp metal. It is supplied at around 650 BHN and does not work harden.
The material feed size must be limited to prevent damage to the blow bars. For Chrome, this is a maximum of 300mm.
High chrome blow bars have a longer lifetime than manganese and provide 3 to 4 times the wear life.
Martensitic Ceramic
The martensitic ceramic blow bars are used mainly in the recycling industry. They are designed to provide the high durability of the martensitic material combined with the excellent abrasive resistance of the ceramic insert.
Martensitic Ceramic blow bars are less susceptible to damage than Chrome so the material feed size is only restricted by the maximum chamber feed size.